

Streamlining Simulation with Logical Expressions in Formula Dependencyīoundary conditions can be dependent on coordinates, time, and monitored parameters (such as goals). A flow resistance law is used to assimilate the flow through the matrix Heat Exchanger, and experimental curves are used for heat transfer from the heat exchanger to the crossing fluid.įlow Simulation drastically simplifies workflow and reduces the numerical model size and computational time. The complex Heat Exchanger matrix is a simplified geometry-based computational model using rectangular volume. When it comes to simulating a system with a gas-liquid crossflow heat exchanger, the Heat Exchanger model in porous media considers experimental Heat versus Flow rate curves in addition to the distributed resistances to fluid flow.

Porous media are treated in Flow Simulation as distributed resistances to fluid flow. Simplifying Workflow with Heat Exchanger Model in Porous Media The fan Derating feature can help you to simulate the different scenarios and optimize the design without the need for multiple physical prototypes or experiments. This is accomplished by lowering revolutions per minute (RPMs), which has the effect of derating (reducing) the fan curve and is simulated using the Derating factor.Īs an example, a printed circuit board (PCB) that supports pulse-width modulation (PWM) can regulate the speed at which its fan rotates to balance cooling capacity and the noise it generates.
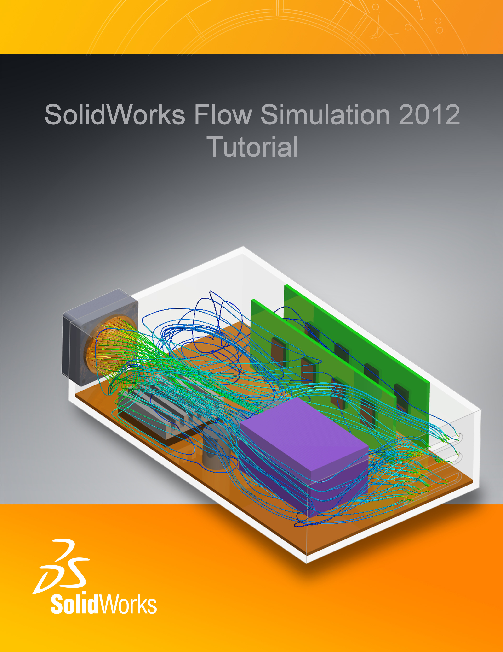
